Borotik is the brand name given to the range of products made by Borotik Wood Industries at Shenbagaramanputhur, Kanyakumari District, Tamil Nadu, India. Borotik principally comprises of eco-friendly and chemically-treated timber derived out of Boron impregnated vacuum seasoned timber. We are the pioneers for wood treatment in India having unique collaboration with Danish Wood Treating Company of Denmark, virtually holding their process expertise, finishing technology and a host of imported equipment from them. Our expertise is reflected on the product quality, customer satisfaction & 99 years guarantee on solid timber which is unmatched in this sector.
BOROTIK India Pvt Ltd produces treated and seasoned rubberwood under the brand name of BOROTIK. Only selected well grown, rubberwood logs are used for manufacture of BOROTIK. The manufacturing process is as given below:-
MANUFACTURING PROCESS OF BOROTIK
SAWING
of felling. The sawn timber is impregnated with wood preservatives within 24 hours of sawing.
CHEMICAL IMPREGNATION PROCESS
a) Initial Vacuum: The freshly sawn green timber is stacked on trolleys and taken inside the cylindrical pressure Vessel. It is hydraulically locked and the vessel is fully evacuated 0.2 bar abs. pressure. This initial vacuum ensures thorough removal of air in both cylinders as well as in the wood. This is to ensure that while applying the chemical solution under pressure, there is no entrapped air within the cells of the timber which can give a counter pressure, thereby ensuring uniform penetration of the preservation solution.
b) Filling phase: In the fully evacuated treatment cylinder, 3% aqueous solution of boron preservative is drawn in, to completely fill the cylinder leaving no air.
c) Pressure phase: The pressure of the preservative solution within the cylinder is raised to 11-12 bar gauge by means of hydraulic pump. The preservative solution, under pressure, is continuously circulated within the Cylinder with the means of High flow rate pump. This ensures continuous and thorough mixing of preservative solution thereby avoiding concentration gradient in the solution. The pressure phase is carried on for 30 minutes.
d) Oscillation Phase: The impregnation process is a modified form of full cell process i.e. the timber is “Green” and the cells are saturated with sap. In order to ensure uniform and thorough absorption of chemical solution by the timber, the preservative solution under circulation is applied a pressure of 11 bar. gauge. and vacuum of 0.3 bar. abs, alternatively for 6 minutes and 3 minutes each. This oscillation of the operating pressure from 11 bar. gauge. to 0.3 bar abs, in quick succession, ensures easy and uniform penetration of the preservative in the body of timber even at timber thickness of 100mm. The time of oscillation phase varies from 60-120 minutes depending on the thickness of timber to be impregnated.
e) Draining: At the end of oscillation process, the preservative solution is drained off and the timber is given a vacuum of 0.2 bar abs for few minutes to remove excess solution from the surface of timber.
f) Dipping: Whenever the impregnated timber is to be stored for several days before seasoning, a suitable fungicide solution is flooded into the cylinder for few minutes to provide Prophylectic protection against sap stain.
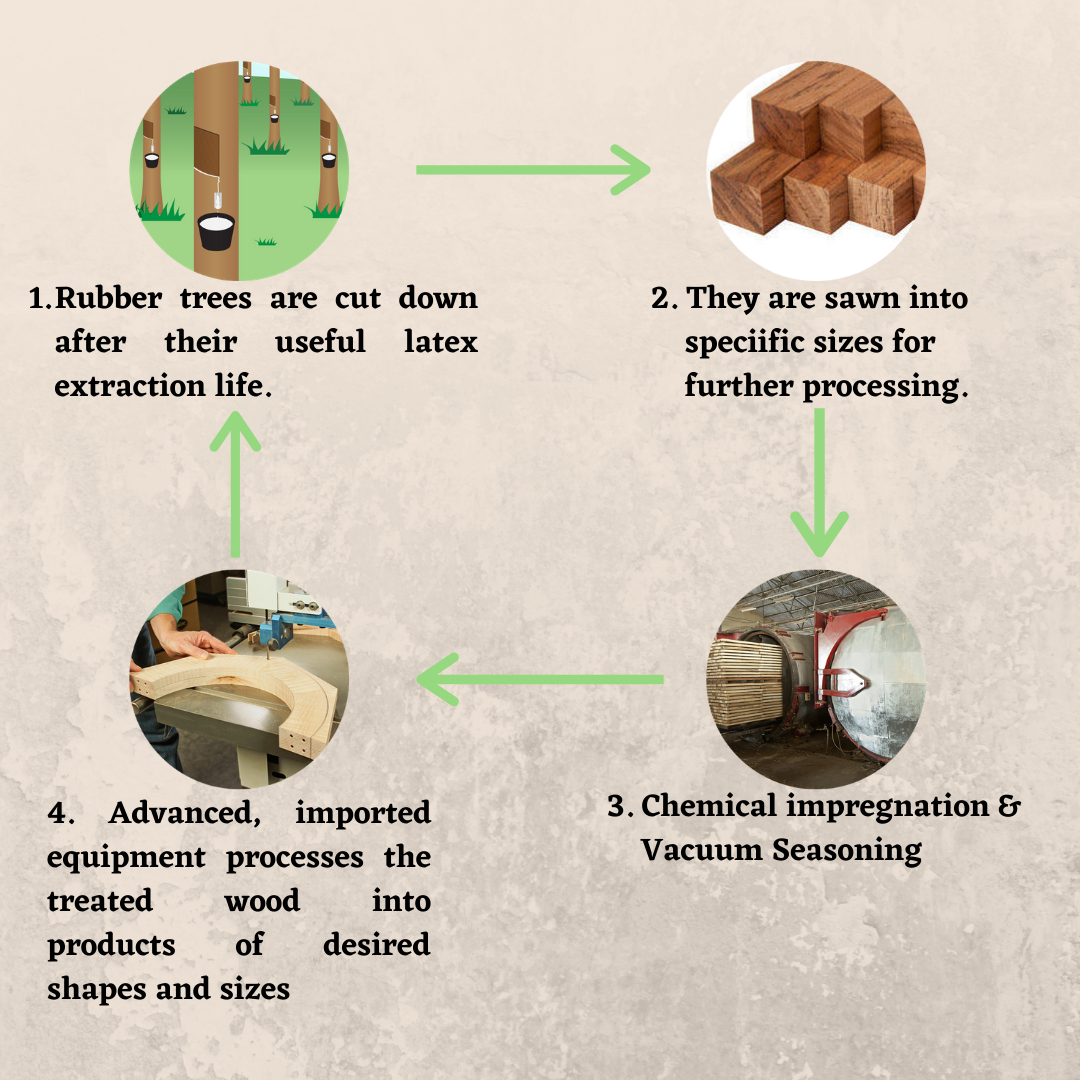
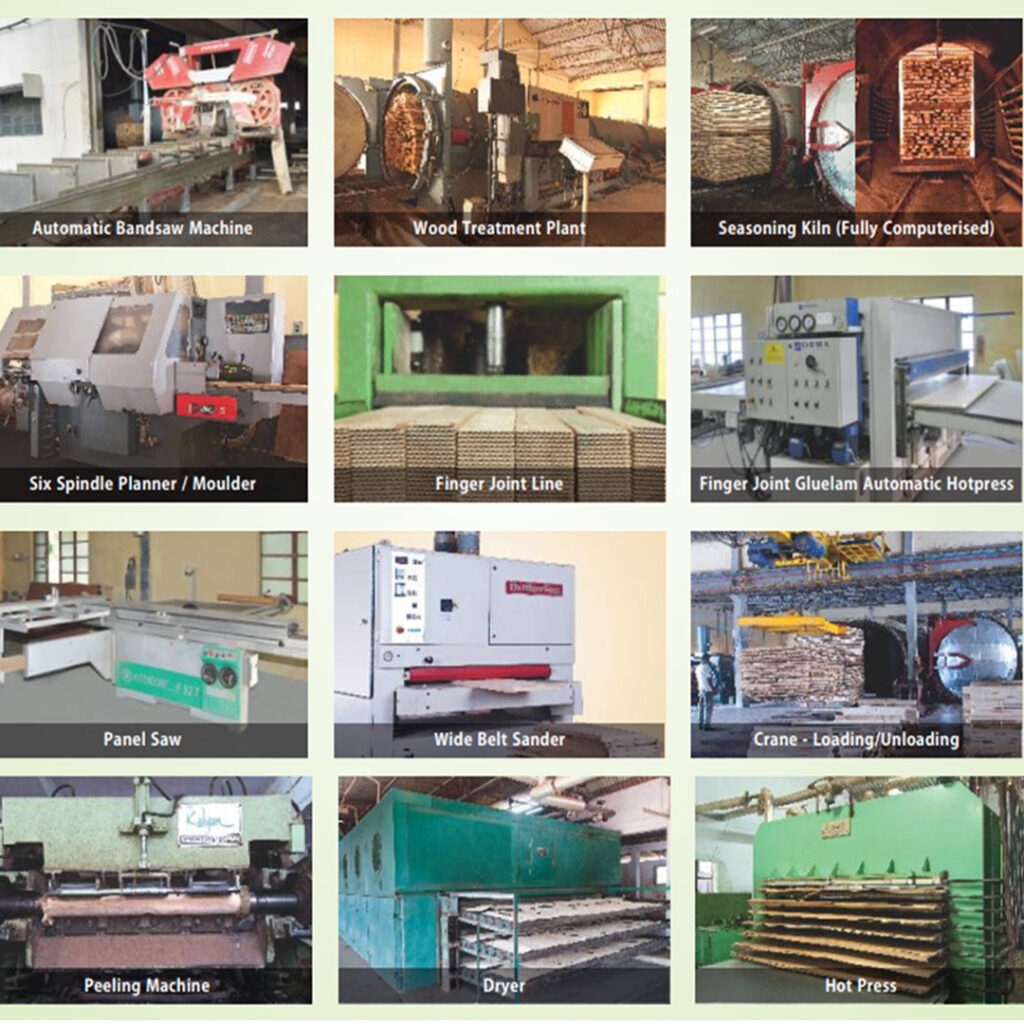
VACCUM SEASONING
a) Charging: The impregnated timber is sticker stacked on trolleys and led into the drying cylinder which is closed and Hydraulically locked. Moisture sensors are connected to 10 randomly selected pieces, whose core moisture content is continuously read and displayed by the PLC.
b) Initial Vacuum: The drying cylinder is evacuated to 0.2 bar. abs.
c) Heating and preconditioning: Heating is supplied to the kiln by circulating pressurized hot water through radiators and circulating the heat through the radiator into the timber packs by fans. Vacuum seasoning is normally carried out at higher temperature then conventional kiln, depending on the species of timber. The temperature in vacuum seasoning is from 70⁰C. to 95⁰C. At the start of the drying process, the lowest temperature is maintained along with the very high RH of 100%. This ensures uniform moisture of all the timber pieces in the drying.
d) Drying phase: The timber drying behavior varies between drying above FSP and below FSP. Vacuum drying is divided into 2 or 3 stages above FSP and 2 or 3 below FSP. Generally the above FSP drying is carried out with lower temperature and higher humidity, progressively increasing the temperature and reducing the humidity. For rubberwood, we are following two drying stages, above FSP i.e. Stage-1 where average MC is more than 40% and Stage-2 where the average MC is less than 40 and more than 30%. Below FSP (which is 30% for rubberwood). The drying is done again in two stages; one when timber moisture is above 15% and second when the timber dries down to final MC of 7%. The entire of drying process is closely controlled with PLC which continuously monitors the average MC of timber and adjusts the drying parameters of the temperature are RH according to the MC. The drying temperature starts from 70⁰C in Stage-1 and gradually increased to 90⁰C in stage-4 with the PLC maintaining accurate control of + or – 1⁰C.